The next Tesla? Why Ohio’s ‘Voltage Valley’ has high hopes.
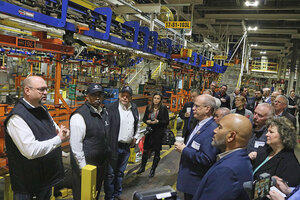
Lordstown Motors executives lead a tour of their Lordstown, Ohio, factory on March 5, 2019. The upstart auto company bought the plant from General Motors last year and is racing to put the first fully-electric pickup truck on the market.
Timmy Broderick/The Christian Science Monitor
Lordstown, Ohio
Steve Burns stands in the cavernous plant that once rolled out thousands of Chevy cars each year and pitches a message of defiant hope: This Rust Belt region’s automotive heyday may actually be in the future.
Mr. Burns is the CEO of Lordstown Motors, which has begun to transform this former General Motors factory into an assembly plant for electric pickup trucks for commercial customers, a first.
Experts say that the electric vehicle (EV) industry has a bright future. Rising concern about climate change means electrification is widely viewed as inevitable. But at a time of tepid consumer demand and fewer federal subsidies nobody knows how far off that giant EV market is and who will control it, and whether an Ohio startup has a shot.
Why We Wrote This
Protecting Earth’s environment is a powerful motive to transform the auto industry. Yet amid tepid sales of electric vehicles, what will it take? We visit an Ohio factory town where this is a high-stakes question.
“We don’t want to just be a product, we want to be a movement. And it’s going to take a movement,” Mr. Burns tells a visiting group of reporters and regional leaders. “We are a little bit David and Goliath.”
Even for larger companies like GM, Ford, and EV-specialist Tesla, there’s no guarantee the U.S. will be a leader in the industry, as rivals in China and elsewhere are also racing to make electric cars and trucks.
Mr. Burns and others here are hoping that this corner of Ohio will be part of a vibrant U.S. industry. Once known as Steel Valley, the Mahoning Valley already has an electric battery testing lab and business incubators focused on energy. GM and South Korea’s LG Chem are building a battery plant right next to Lordstown Motors (though the batteries won’t be compatible with its Endurance pickup). Youngstown State University is creating a training center for students interested in working for the startup.
Local leaders are now trying to rebrand the area as Voltage Valley. And Lordstown plans to build 20,000 electric trucks in 2021, with a future goal of 420,000 vehicles a year.
But that momentum depends on government support. The Trump administration is rolling back emissions standards and nixed a key EV tax-credit expansion late last year. It also proposed a budget that would kill an Energy Department loan program that fueled Tesla’s rise – one that Lordstown Motors has been eyeing.
Moreover, even as the cost of car batteries has fallen, EVs still cost more than gasoline-powered cars and trucks, which is why the industry needs government handouts. The Endurance is expected to cost $52,000 before tax credits.
“We are all standing on this stage because of Tesla, right? But what launched Tesla was a stodgy government loan,” says Mr. Burns, who has hired several former Tesla executives.
“Consistency is what you need”
Born in the wake of the 2008 financial crisis, the EV tax credit catalyzed the industry’s growth. Tesla and GM recently surpassed the 200,000-vehicle sales marker, which means their EVs no longer qualify for full credits. Both companies lobbied unsuccessfully to lift the cap in last year’s congressional funding bill.
“We have a well-established history of how you get these boom-bust cycles when you offer incentives and then withdraw them and offer them again. Consistency is what you need if you want a steadily- and fast-growing industry,” says Chris Nelder, who manages the Rocky Mountain Institute’s EV-Grid Initiative.
China also introduced electric vehicle subsidies about a decade ago. When the government trimmed those credits last July, sales plummeted and now the cuts are being reconsidered.
Mike Carr of the EV Drive Coalition, an industry lobbying group, says U.S. policy should also be supportive. “The market doesn’t value the zero emission benefits. It doesn’t value the climate benefits. It doesn’t value all the societal benefits that are brought by these vehicles,” he says.
A higher sticker price is one handicap, though some experts predict the gap could be closed in a few years. Another hurdle is charging infrastructure: Outside of California, not much is being built. As a result, the U.S. EV market is still only 1.4% of new vehicle sales, which topped 17 million in 2019.
How former GM workers feel
Doubts are high even among local auto workers who for decades built Chevrolet sedans in this community of 3,200 people. The United Auto Workers opposed the sale of the complex, which employed nearly 1,500 workers, to Lordstown Motors.
Mr. Burns pledges a union plant, and says his priority is to hire former GM workers at wages competitive with other auto plants. But most of those workers either transferred or retired when GM closed the plant.
“Would I be interested in going back in there and working? I doubt it,” says Matt Moorhead, who worked at the Lordstown GM plant since 1995. “I can do the work, but just with everything that happened – my job was taken away from me, and I’m not going to go back for half the wage.”
Mr. Moorhead is not alone. Everyone in the region knows someone who worked at the Lordstown plant. At a union hall a mile from the plant, workers say they only know two or three former colleagues who have applied for jobs at the retooled plant.
Ultimately, Lordstown Motors’ success may depend on whether rivals like Tesla decide its future lies in the U.S., says Mr. Carr. If final assembly of vehicles migrates to China or Europe, suppliers will follow, and without their technology it’s hard to see a bright future here for an electrification hub.
“The industry is at a real inflection point [in the U.S.],” he says. “We risk losing momentum and thus market share to China.”
Mr. Burns plans to hire 400 workers by late summer and ramp up operations from there.
“That factory can produce more vehicles than Tesla’s. It’s twice the size. It’s very capable,” he says in a phone interview. “I think the Midwest workers are as capable as anybody in the world at building cars. We think we’ve got a great recipe and a great demand for a vehicle like this. But it’s going to take hard work.”