Recirculating aquaculture systems: The future of fish farming?
Recirculating aquaculture systems cut the pollution and disease that occur in current fish farming operations. Many see it as the future of the industry.
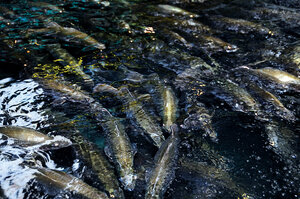
Australian barramundi churn water that is filtered and recycled at Australis Aquaculture in Turners Falls, Mass. The company raises the fish using a recirculating aquaculture system.
Courtesy of Australis Aquaculture
Shepherdstown, W.Va.
Inside what looks like a plastic-roofed greenhouse sitting in an old cow pasture are six round, 1,500-gallon tanks (imagine kiddie pools that are eight feet deep), each holding a few hundred rainbow trout. A tangled network of PVC pipes – some as thick as tree trunks, others as slender as pool cues – traces crooked patterns in the cramped space, which is alive with the sound of whirring motors and lots of water, dripping, bubbling, and gushing steadily through the whole convoluted system.
It looks like an ambitious science-fair project. But these are recirculating aquaculture systems at the nonprofit Conservation Fund's Freshwater Institute, which has researched water use and conservation since 1987. And they represent an exciting new development in food sustainability.
Recirculating aquaculture systems, or RAS, are closed-loop production systems that continuously filter and recycle water, enabling large-scale fish farming that requires a small amount of water and releases little or no pollution.
About 99.75 percent of the water in each unit is continuously cleaned and returned to the fish tanks. Manure filtered from the water during the recycling process is used as fertilizer on nearby farm fields. The nutrient-rich water can also be used to feed vegetables and herbs in large-scale aquaponics systems, which in turn filter the water for reuse.
One of RAS's biggest benefits is its small "water footprint," which opens the door to commercial fish production in areas with limited water resources. (The technology is proven for both fresh- and saltwater species).
As efficient as before, but cleaner
The closed-loop RAS design also addresses several major environmental concerns associated with traditional aquaculture, particularly ocean-based "net pen" fish farms where saltwater species are corralled in offshore enclosures.
At these densely stocked net pen farms, concentrated fish waste flows directly into the surrounding ocean. Industry critics often cite a European study that concluded that the pollution from an average salmon farm is equivalent to discharging raw human sewage from a town of several thousand people.
In addition to fish waste, antibiotics and other chemicals administered to the farmed fish can flow directly into the surrounding water. Disease is another environmental concern associated with net pen farming, as the crowded fish are susceptible to outbreaks that can spread to wild populations.
When Steve Summerfelt, who directs aquaculture systems research at Freshwater, began working on RAS development in 1992, his goal was to demonstrate that recirculating systems could produce healthy fish as quickly as traditional production methods.
After that was accomplished within a few years, his research – largely funded by the US Department of Agriculture – has focused on expanding RAS technology to larger scales that remain cost-competitive with other production methods.
That's no small challenge when competing against offshore fish farmers who don't pay for their water or face the constant expense of cleaning the water for reuse. But the efficient, cost-competitive RAS technologies developed at Freshwater and elsewhere are catching the interest of commercial fish farmers.
For example, Dr. Summerfelt says, his organization has been talking with about half a dozen fish farms that are considering investing between $5 million and $50 million in RAS production.
"Right now, [RAS] systems are not producing a tremendous amount of fish for the US," he says. "It's going to take these $5 million to $50 million investments to start seeing it happen."
Obstacles include the newness of proven, commercial-scale RAS technologies – which makes lenders cautious – and the large amount of capital required, Summerfelt says. The current recession, which has restricted access to credit, has also slowed the adoption of commercial RAS aquaculture production even further, he adds.
Coinciding with the development of cost-competitive, large-scale RAS technology has been the development of alternative fish feeds, which use plant-based proteins to largely or entirely replace the fish meal and fish oil from wild-caught fish that are used in conventional fish feeds for carnivorous farmed fish such as salmon and trout.
Several factors have driven the development of alternative feeds, said Rick Barrows, a fish physiologist with the USDA Agricultural Research Service. One is supply and demand. Global production of fish meal has remained relatively stable for decades, while demand from aquaculture has grown immensely over the past 20 years. With many of the world's oceanic fisheries harvested at or beyond sustainable levels, there's little capacity to expand fish meal production. By some estimates, raising one pound of farmed salmon on a fish meal-based diet requires three to four pounds of wild-caught fish, which produces an adverse ecological impact.
Alternative feeds, says Dr. Barrows, also offer improved food security, because conventional feeds can contaminate farmed fish with toxics like PCBs that sometimes accumulate in wild fish populations harvested for fish meal.
Barrows, who has worked on alternative aquaculture feed research for nearly 30 years, said a USDA-developed feed formula using corn, soy, wheat, and barley protein has been perfected within the past year. This has been shown to perform as well, or even better, than fish meal-based feeds.
A niche market, for now
For researchers such as Summerfelt and Barrows, it's exciting to see RAS production and alternative fish feeds begin to take hold in commercial aquaculture – thanks to the development of suitable, cost-competitive technologies and consumer demand.
"There are a lot of things that have come together," Summerfelt points out. Currently, most commercial fish farmers who have successfully adapted these sustainable techniques operate in high-value niches of the industry, raising fish such as arctic char, hybrid striped bass, cobia, and others that sell at a premium price, thereby softening the blow of RAS's significant upfront costs.
Although commercial RAS production in the United States remains in its infancy, the conditions are right for rapid growth in a global aquaculture industry that itself is growing at a phenomenal rate – more than 8 percent annually each year since 1985.
"People get it that [sustainability] is good business sense," said Josh Goldman, founder and CEO of Australis Aquaculture, a company at the forefront of sustainable American aquaculture.
Australis, based in Turners Falls, Mass., has been raising barramundi (also called Asian sea bass) with RAS since 2004. The company recycles more than 99 percent of its water and uses a grain-based feed adapted from a formula developed by Australian scientists to produce about 2 million pounds of barramundi each year, Mr. Goldman says.
The start-up cost for the 92,000-square-foot facility – one of the largest indoor RAS producers in the world – was about $15 million. Demand for Australis's barramundi, is "growing nicely," Goldman says, with sales doubling from 2008 to 2009.
Marianne Cufone, director of the fish program for Food & Water Watch, a consumer advocacy group, believes that this trend will continue with increased awareness of RAS's environmental benefits – a goal toward which her organization is working. "I have high hopes," she says, "that this will take off very soon."
-----