Icephobic coating: How researchers made the most effective ice-proofer yet
A research team from the University of Michigan has developed a strategy for creating rubbery coatings that require no more than a light breeze for ice to slide off.
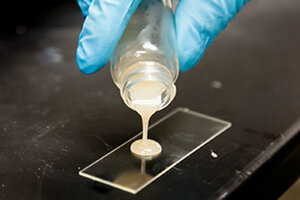
Kevin Golovin, a graduate student in Materials Science and Engineering at the University of Michigan, demonstrates a new rubbery material that can create ice repelling, or "icephobic" coatings on a variety of materials, such as windshields or ship hulls.
Evan Dougherty/University of Michigan
A team of University of Michigan researchers has developed a new “icephobic” material that could improve and simplify the process of ice removal across a variety of surfaces.
For most of us, ice on sidewalks or windshields is an inconvenience, but in certain industries, the frozen substance can prove extremely hazardous. By using a different method for developing icephobic coatings, the researchers may have found a way to make ice on airplanes, power lines, wind turbines, and other surfaces easier to remove.
The new process has led to the creation of rubbery repellants that are energy efficient and extremely effective at clearing away ice. Whereas previous ice removal efforts were focused on creating chemically water-repellant materials, the Michigan scientists found that the use of rubbery polymers was more practical at pushing off the frozen substance.
“Researchers had been trying for years to dial down ice adhesion strength with chemistry, making more and more water-repellent surfaces,” said Michigan graduate student Kevin Golovin, one of the participants on the project, in a university release on the discovery. “We’ve discovered a new knob to turn, using physics to change the mechanics of how ice breaks free from a surface.”
In the release, Mr. Golovin explains that regardless of water resistance, when two rigid materials such as ice and glass stick together, much force is needed to break the bond between them. But if a solid material like ice is on a rubbery surface, a phenomenon known as interfacial cavitation means that very little force is needed in order to break off the hard ice.
“Nobody had explored the idea that rubberiness can reduce ice adhesion,” associate engineering professor Anish Tuteja said. “Ice is frozen water, so people assumed that ice repelling surfaces had to also repel water. That was very limiting.”
In their research paper, published in Science Advances, the scientists defined icephobic surfaces as those with an ice adhesion pressure below 100 kilopascals (kPa), but that successful ice removal requires a stress level below 20 kPa. Through testing more than 100 elastomers - polymers with properties of both solids and liquids - the researchers were able to develop some with ice adhesion strengths as low as 4 kPa.
During durability trials for some of the elastomers outdoors in Ann Arbor, Mich. winters, the team saw ice removed from a window treated with the coating by only a light breeze. And after months of keeping the polymer outside in the cold, its ice adhesion levels were the same as before testing began, showing the potential stability of the materials.
The researchers are also able to adjust the consistency and durability of the coating for different situations. The university’s release states that softer surfaces aren’t as tough but are better at repelling ice than harder surfaces that can last longer. The variability in the coatings’ compositions could allow for their application across a wide array of fields and industries.
“The great thing about our approach is that it’s easy to fine-tune it for any given application,” Golovin said.
Although commercial use of the elastomers could take a few years, the potential for the cost, time, and energy savings associated with their use should prove beneficial in areas such as transportation and power generation. The researches expect the new materials' first application will be on frozen food containers, to help keep them from sticking together.
“Using this technology in places like cars and airplanes will be very complex because of the stringent durability and safety requirements, but we’re working on it,” Mr. Tuteja said.